Types of frozen food packaging
Frozen food packaging is designed to protect and preserve the quality of frozen products while providing convenience for consumers. There are various types of packaging used for frozen foods, each catering to specific needs and product characteristics. Here are some common types of frozen food packaging:
- Flexible Bags and Pouches:
- Applications: Vegetables, fruits, seafood, and frozen meals.
- Features: Flexible pouches with seal closures. Often used for single servings or larger quantities.
- Frozen Food Boxes and Cartons:
- Applications: Frozen pizzas, frozen desserts.
- Features: Rigid cardboard or paperboard packaging. May include additional features like a window for product visibility.
- Vacuum Packaging:
- Applications: Meat, poultry, and certain frozen fruits and vegetables.
- Features: Removal of air to prevent freezer burn and maintain product freshness.
- Frozen Food Trays with Lids:
- Applications: Ready-to-cook frozen meals.
- Features: Rigid plastic trays with a tight-fitting lid for easy cooking and storage.
- Stand-Up Pouches:
- Applications: Frozen snacks, vegetables, and fruits.
- Features: Convenient stand-up design with resealable zippers. Provides good product visibility.
- Frozen Food Sleeves:
- Applications: Frozen desserts, ice cream bars.
- Features: Sleek sleeves for individual or multipack frozen treats.
- Frozen Food Wrappers:
- Applications: Individual frozen items like hot dogs, hamburgers.
- Features: Single-use wrappers for easy storage and handling.
- Shrink Film Packaging:
- Applications: Frozen meat cuts, poultry.
- Features: Shrink-wrap packaging provides a tight seal, protecting against freezer burn.
- Aluminum Foil Packaging:
- Applications: Frozen casseroles, baked goods.
- Features: Provides a barrier against light, moisture, and odors.
- Frozen Food Bags with Zipper Seal:
- Applications: Frozen fruits, vegetables, and snacks.
- Features: Resealable bags for convenient portion control and easy storage.
- Foil Containers with Lids:
- Applications: Frozen entrees, casseroles.
- Features: Aluminum foil containers with matching lids for freezer-to-oven convenience.
- Modified Atmosphere Packaging (MAP):
- Applications: A variety of frozen foods.
- Features: Alters the atmosphere inside the packaging to extend shelf life.
When choosing frozen food packaging, factors such as the type of food, desired shelf life, convenience features, and regulatory requirements must be considered. Packaging design should prioritize maintaining product quality during freezing, storage, and transportation while providing a positive consumer experience.
Why choose flexible packaging bag for frozen food?
Flexible packaging for frozen food offers several advantages, making it a popular choice for manufacturers, retailers, and consumers. Here are some reasons why flexible packaging is commonly chosen for frozen food:
- Versatility:
- Adaptability: Flexible packaging can be customized to suit various frozen food products, including vegetables, fruits, seafood, and ready-to-cook meals.
- Convenience:
- Ease of Handling: Flexible packaging is lightweight and easy to handle, both for manufacturers during production and for consumers when storing or opening the package.
- Cost-Effectiveness:
- Material Efficiency: The efficient use of materials in flexible packaging can lead to cost savings in terms of production and transportation compared to traditional rigid packaging.
- Extended Shelf Life:
- Barrier Properties: Flexible packaging can be designed with multiple layers, providing excellent barrier properties against light, oxygen, and moisture. This helps to extend the shelf life of frozen food.
- Reduced Environmental Impact:
- Lightweight Design: The lightweight nature of flexible packaging reduces transportation costs and the overall environmental footprint. Additionally, some flexible packaging materials are recyclable or made from sustainable sources.
- Customization:
- Brand Visibility: Flexible packaging allows for customizable printing and branding options, helping to enhance brand visibility on the retail shelf.
- Resealable Features:
- Consumer Convenience: Many flexible packaging options include resealable features such as zippers or seals, allowing consumers to reseal the package after opening. This helps maintain product freshness and reduces food waste.
- Innovative Designs:
- Creativity in Design: Flexible packaging allows for innovative and creative designs, attracting consumer attention and differentiating products in a competitive market.
- Temperature Resistance:
- Freezer Compatibility: Flexible packaging materials are designed to withstand low temperatures, making them suitable for frozen food storage.
- Portion Control:
- Single-Serving Options: Flexible packaging can be designed for single-serving portions, providing consumers with convenient options for portion control.
- Easy Storage:
- Space Efficiency: Flexible packaging can be designed to collapse as the product is consumed, making it efficient for storage in both home freezers and retail settings.
- Ease of Distribution:
- Compact Transportation: The flexibility and space efficiency of flexible packaging contribute to cost-effective transportation and distribution.
Ultimately, the choice of flexible packaging for frozen food depends on the specific requirements of the product, brand strategy, and consumer preferences. Manufacturers often find that flexible packaging offers a combination of practicality, cost efficiency, and environmental considerations, making it a preferred option for packaging frozen foods.
Plastic frozen food bag
Plastic frozen food bags offer several advantages, but they also come with certain disadvantages. Here's an overview of the pros and cons of using plastic frozen food bags:
Advantages:
- Versatility: Plastic frozen food bags are versatile and can be adapted to various shapes and sizes, accommodating different frozen food products.
- Cost-Effective: Plastic is often more cost-effective than some alternative materials, contributing to overall cost savings in production.
- Lightweight: Plastic bags are lightweight, reducing transportation costs and making them easier for consumers to handle.
- Transparency: Many plastic bags are transparent, allowing consumers to see the contents easily and assess the quality of the frozen food.
- Customization: Plastic bags can be easily customized through printing, allowing for branding, product information, and promotional elements.
- Sealing Properties: Plastic bags provide effective sealing, helping to protect frozen food from external elements such as moisture and air, which can contribute to freezer burn.
- Resealable Features: Some plastic frozen food bags come with resealable features, allowing consumers to reseal the package after opening, maintaining product freshness.
- Durability: Plastic bags are durable and can withstand the freezing temperatures required for storing frozen food.
- Convenience: Plastic bags are often convenient for consumers to open, handle, and dispose of after use.
- Recyclability: Depending on the type of plastic used, some frozen food bags can be recyclable.
Disadvantages:
- Environmental Impact: Plastic is associated with environmental concerns, including pollution and issues related to disposal. Many traditional plastics are not easily biodegradable.
- Limited Barrier Properties: While plastic provides a barrier against moisture, it may not offer as effective a barrier against oxygen and light as some other packaging materials.
- Not Suitable for All Products: Certain frozen food products may not be suitable for plastic packaging due to specific requirements for protection against light, oxygen, or other factors.
- Potential for Freezer Burn: In some cases, plastic bags may not provide sufficient protection against freezer burn, which can affect the quality of frozen food over time.
- Permeability: Depending on the type of plastic used, there may be permeability to odors or flavors, impacting the taste and quality of the frozen food.
- Recycling Challenges: Some plastic materials used in frozen food bags may face challenges in the recycling process, and not all regions have robust recycling systems for certain types of plastics.
- Plastic Waste: Improper disposal of plastic bags contributes to plastic waste, which can have detrimental effects on the environment.
It's important for manufacturers and consumers to weigh these advantages and disadvantages based on specific needs, product characteristics, and sustainability goals. Innovations in packaging technology and the development of more sustainable materials are continually evolving to address some of the challenges associated with traditional plastic packaging.
How about transparent frozen food packaging bag?
Transparent frozen food packaging bags are commonly used for a variety of frozen food products. The transparency of these bags allows consumers to see the contents easily and assess the quality of the frozen food. Here are some features and considerations related to transparent frozen food packaging bags:
Features:
- Product Visibility: The primary advantage of transparent packaging is that it provides a clear view of the frozen food inside. This can be particularly important for products with visual appeal, such as frozen fruits, vegetables, or prepared meals.
- Brand Visibility: Transparent bags offer an opportunity for brand visibility and product marketing. Brands can showcase the quality and freshness of their frozen food products through the clear packaging.
- Consumer Confidence: Being able to see the contents of the packaging instills confidence in consumers. They can easily check for any signs of damage, ice crystals, or other factors that may affect the product's quality.
- Printing and Labeling Options: While the bag itself is transparent, manufacturers can still incorporate printed labels, logos, and product information to enhance branding and communicate essential details to consumers.
- Convenience: Transparent bags are often convenient for consumers, as they can quickly identify the product they are looking for without having to read labels in detail.
- Customization: Transparent bags can be customized in terms of size, shape, and printing to meet specific packaging requirements and branding goals.
- Resealable Features: Some transparent frozen food packaging bags come with resealable features, allowing consumers to reseal the bag after opening. This helps maintain product freshness and prevents freezer burn.
- Material Options: Transparent bags can be made from various materials, including clear plastic films or laminates that provide the necessary barrier properties to protect against moisture and external elements.
Considerations:
- Barrier Properties: While transparency is a key feature, it's crucial to ensure that the packaging material provides sufficient barrier properties to protect the frozen food from factors like moisture, air, and light.
- Freezer Compatibility: The material used for transparent frozen food bags should be suitable for freezer storage and be able to withstand low temperatures without becoming brittle.
- Sustainability: Consideration should be given to the sustainability of the materials used. Manufacturers may opt for recyclable or eco-friendly options to align with sustainability goals.
- Printing Technology: High-quality printing technology is important for adding branding and product information without compromising the transparency of the packaging.
Transparent frozen food packaging bags are commonly used for a range of products, from frozen fruits and vegetables to prepared meals. They offer a balance between product visibility, branding opportunities, and the necessary protective features to ensure the quality and freshness of the frozen food.
Is frozen food packaging bag recyclable?
The recyclability of frozen food packaging bags depends on the specific materials used in their construction. Different types of plastics and multilayer films are common materials for frozen food packaging, and their recyclability can vary. Here are some considerations regarding the recyclability of frozen food packaging bags:
- Monomaterial Bags: Some frozen food packaging bags are designed with a single type of plastic, making them more easily recyclable. Polyethylene (PE) is a commonly used plastic that is more widely accepted for recycling.
- Multilayer Films: Many frozen food packaging bags are made from multilayer films, combining different materials for specific barrier properties. While these films can enhance product protection, they may pose challenges for recycling due to the difficulty of separating the layers.
- Recycling Symbols: Check for recycling symbols on the packaging, usually found near the bottom. These symbols, such as the chasing arrows with a number inside, indicate the type of plastic used. However, the presence of a recycling symbol does not guarantee that the material is accepted in all recycling programs.
- Local Recycling Guidelines: Recycling capabilities vary by location, and different municipalities may have different rules about which types of plastics they accept for recycling. It's essential to check with local recycling facilities to understand what materials they can process.
- Collection Programs: Some areas may have specialized collection programs or drop-off locations for specific types of flexible plastic packaging, including frozen food bags. Manufacturers and retailers may participate in such programs to encourage recycling.
- Recyclability Labels: Some manufacturers provide information on the recyclability of their packaging, including details about whether the packaging is widely recyclable or if it requires specific recycling programs.
- Sustainability Initiatives: In response to growing environmental concerns, there is an industry push toward developing more sustainable and recyclable packaging solutions. Some manufacturers are exploring alternatives that prioritize recyclability and eco-friendly materials.
- Plastic Film Recycling: Some grocery stores and retail locations have plastic film recycling bins where consumers can deposit certain types of flexible plastic packaging, including bags. These programs often accept clean and dry plastic films.
It's important to note that contamination, such as food residues or non-recyclable materials mixed with recyclables, can hinder the recycling process. Consumers and manufacturers should follow local guidelines, be aware of recycling limitations, and actively participate in programs that support plastic film recycling initiatives. Additionally, advancements in packaging technology continue to explore more sustainable and recyclable solutions for frozen food packaging.
Custom frozen food packaging
Creating custom frozen food packaging bags involves tailoring the design, materials, and features to meet the specific needs of the frozen food product and the brand. Here's a step-by-step guide to creating custom frozen food packaging bags:
- Define Packaging Objectives:
- Clearly outline the objectives of the packaging, including product protection, shelf appeal, and branding goals.
- Understand Product Characteristics:
- Consider the specific characteristics of the frozen food product, such as size, shape, weight, and whether it requires specific temperature-resistant materials.
- Select Suitable Materials:
- Choose materials with excellent barrier properties to protect against moisture, air, and freezer burn.
- Explore sustainable options, such as recyclable or biodegradable materials, based on environmental considerations.
- Customize Dimensions and Shape:
- Determine the appropriate dimensions and shape of the packaging to accommodate the specific product size and volume.
- Incorporate Branding Elements:
- Design custom graphics, logos, and other branding elements to be printed on the packaging. Consider color schemes that align with the brand identity.
- Add Transparent Windows:
- Include transparent windows in the packaging to showcase the frozen food product and allow consumers to see the contents.
- Integrate Resealable Features:
- Add resealable features, such as zippers or seals, to enhance consumer convenience and maintain product freshness.
- Choose Dispensing Systems:
- Customize dispensing systems based on the product type. Consider options like easy-pour spouts or resealable closures for frozen snacks.
- Consider Special Features:
- Incorporate special features, such as tear notches, handles, or hang holes, to enhance functionality and convenience.
- Ensure Tamper-Evident Seals:
- Include tamper-evident seals to provide consumers with confidence in the safety and integrity of the frozen food product.
- Create Custom Labels and Stickers:
- Develop custom labels or stickers for additional product information, recipes, or promotional messages.
- Check Environmental Considerations:
- Communicate any environmentally friendly features of the packaging, emphasizing recyclability or the use of sustainable materials.
- Ensure Regulatory Compliance:
- Verify that the custom packaging complies with food safety regulations and meets labeling requirements.
- Conduct Packaging Testing:
- Perform testing to ensure that the custom packaging meets functional requirements, including freeze-thaw resistance, durability, and shelf stability.
- Collaborate with Packaging Experts:
- Work closely with packaging experts or suppliers to explore innovative solutions, discuss design options, and obtain samples for testing.
- Evaluate Cost Considerations:
- Consider the cost implications of the custom packaging design, including materials, printing, and additional features.
- Review and Iterate:
- Review the custom packaging design iteratively, considering feedback from stakeholders and making adjustments as needed.
- Production and Distribution:
- Once the design is finalized, proceed with the production of custom frozen food packaging bags and coordinate distribution logistics.
By following these steps, manufacturers can create custom frozen food packaging bags that effectively protect the product, appeal to consumers, and align with brand goals. Collaboration with packaging experts and suppliers is crucial throughout the design and production process to ensure optimal results.
Must a Holes in freezer packaging bag?
No, holes in freezer packaging bags are not intended and are considered a defect. The design of freezer packaging is meant to create a sealed and protective environment to prevent issues such as freezer burn, contamination, and deterioration of the frozen food. Holes in the packaging compromise its ability to provide an effective barrier against external factors, and they are not part of the standard design.
Here are reasons why holes in freezer packaging bags are not desirable:
- Preservation of Quality:
- The primary purpose of freezer packaging is to preserve the quality of the frozen food. Holes can allow air to enter, leading to freezer burn and dehydration of the food, negatively impacting its texture, flavor, and nutritional value.
- Contamination Risk:
- Holes in the packaging can expose the frozen food to contaminants, reducing the overall safety and quality of the product.
- Temperature Maintenance:
- The integrity of the packaging is crucial for maintaining the desired temperature inside the bag. Holes can compromise the insulation, leading to temperature fluctuations that affect the frozen food.
- Consumer Confidence:
- Consumers expect freezer packaging to be intact and free from defects. Holes can undermine consumer confidence in the safety and quality of the product.
- Loss of Product:
- Holes in the packaging may lead to product spillage or leakage, causing a loss of the frozen food and potential waste.
To ensure the effectiveness of freezer packaging, manufacturers implement quality control measures during the production process. Quality checks include assessing the integrity of the packaging for any signs of damage, holes, or defects. It's crucial for manufacturers to use durable and suitable materials that can withstand freezing temperatures without compromising their integrity.
If consumers encounter freezer packaging with holes, it is advisable to inspect the product carefully for any signs of compromise, and if necessary, contact the manufacturer or retailer for resolution. Additionally, proper storage conditions by both manufacturers and consumers are essential to prevent damage to the packaging and maintain the quality of the frozen food.
When packaging which products, it is better to have a air hole on the packaging bag?
The decision to include air holes in packaging depends on the specific characteristics of the product being packaged and the desired packaging goals. Air holes, also known as ventilation holes, can be beneficial in certain situations where the product requires airflow or the release of gases. Here are some products for which air holes might be considered:
- Fresh Produce:
- Fruits and vegetables, such as lettuce, mushrooms, or berries, may benefit from air holes to maintain freshness by allowing air circulation and preventing condensation.
- Bakery Products:
- Bread or baked goods may be packaged with air holes to help maintain their texture and prevent moisture buildup.
- Live Plants:
- Potted plants or flowers may require air holes for ventilation during transportation, especially if they are in sealed packaging.
- Perishable Foods:
- Some perishable foods, like certain types of cheeses or fermented products, may benefit from air holes to allow gases produced during the fermentation process to escape.
- Dairy Products:
- Dairy products, such as certain types of cheeses, may require air holes to facilitate proper aging and prevent the buildup of excess moisture.
- Fresh Seafood:
- Certain types of seafood, like live shellfish or fresh fish, may be packaged with air holes to ensure oxygen exchange and maintain product quality.
- Plants or Seeds:
- Packages containing seeds or live plants may have air holes to allow for air exchange and prevent the buildup of excess moisture.
- Pet Food:
- Some types of pet food, particularly those with high moisture content, may be packaged with air holes to prevent spoilage.
It's important to note that while air holes can be beneficial for certain products, they may not be suitable for others. For example, frozen food packaging is designed to be airtight to prevent freezer burn and maintain product quality. Additionally, air holes in packaging can impact shelf life, so careful consideration is required based on the specific needs of the product.
When considering the inclusion of air holes, manufacturers should conduct thorough testing to ensure that the packaging design meets the requirements of the product and does not compromise its quality, safety, or shelf life. The decision to include air holes should be based on a balance between the need for ventilation and the preservation of the product's freshness and quality.
How about the flexible bag material option for packaging frozen food?
Flexible bag materials for packaging frozen food need to provide effective barrier properties against moisture, air, and other external elements to maintain the quality and safety of the frozen products. Here are some common flexible bag material options used for packaging frozen food:
- Polyethylene (PE):
- High-Density Polyethylene (HDPE): Offers good strength and durability, suitable for frozen food bags and liners.
- Low-Density Polyethylene (LDPE): Provides flexibility and sealability, commonly used in various types of frozen food packaging.
- Polypropylene (PP):
- Known for its high-temperature resistance and strength, PP is used in frozen food bags, pouches, and packaging films.
- Polyester (PET):
- PET is transparent, rigid, and has good barrier properties. It is used for frozen food bags, especially those requiring visibility of the product.
- Nylon (Polyamide):
- Nylon is used in multilayer films for frozen food packaging, providing excellent barrier properties against oxygen and moisture.
- EVOH (Ethylene Vinyl Alcohol):
- EVOH is often incorporated into multilayer films for its excellent gas barrier properties, helping to prevent oxygen penetration and extend shelf life.
- Aluminum Foil Laminates:
- Multilayer films that include aluminum foil provide effective barriers against light, oxygen, and moisture. Aluminum foil laminates are used in various frozen food packaging applications.
- Vacuum Packaging Films:
- Specialized films designed for vacuum packaging help remove air from the package, preventing freezer burn and maintaining product freshness.
- Biodegradable and Compostable Films:
- Some manufacturers use biodegradable or compostable materials for flexible frozen food packaging to address environmental concerns. These materials may include bio-based plastics or compostable films.
- Polyethylene Terephthalate Glycol (PETG):
- PETG is a transparent and rigid material used for frozen food packaging where visibility of the product is important.
- Specialized Barrier Films:
- Advanced barrier films may include layers designed to provide specific properties such as high oxygen, water, or light barrier, tailored to the needs of the frozen food being packaged.
When choosing flexible bag materials for packaging frozen food, it's essential to consider factors such as the specific requirements of the product, the desired shelf life, and the environmental impact of the materials. Manufacturers often select materials based on their ability to withstand freezing temperatures, maintain product freshness, and comply with food safety regulations. Additionally, advancements in material science continue to lead to innovations in flexible packaging options for frozen foods.
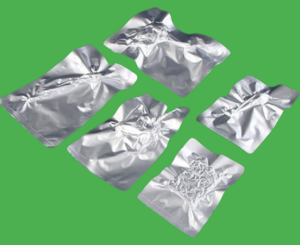
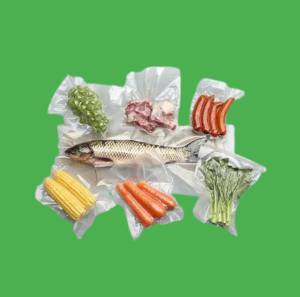

Cost of frozen food packaging pouch?
The cost of frozen food packaging pouches can vary based on several factors, including the materials used, the size and dimensions of the pouch, the printing and customization requirements, and the quantity ordered. Additionally, factors such as the complexity of the design, the inclusion of special features, and the chosen supplier or manufacturer can influence the overall cost. Here are some key factors that contribute to the cost of frozen food packaging pouches:
- Material Type:
- The choice of material significantly affects the cost. Common materials include polyethylene (PE), polypropylene (PP), polyester (PET), nylon, aluminum foil, and various multilayer films. High-barrier films or specialty materials may be more expensive.
- Pouch Size and Dimensions:
- The size and dimensions of the pouch impact the amount of material required for production. Larger pouches typically require more material and may result in higher costs.
- Printing and Customization:
- Custom printing, branding, and special features (e.g., transparent windows, resealable zippers, or spouts) can contribute to the overall cost. The complexity of the printing and customization process may also influence pricing.
- Order Quantity:
- The quantity ordered has a direct impact on the unit cost. Larger production runs often result in lower unit costs due to economies of scale.
- Design Complexity:
- The complexity of the pouch design, including intricate graphics, multiple colors, and detailed artwork, can affect printing costs and overall production expenses.
- Special Features:
- The inclusion of special features such as resealable closures, spouts, or specialized closures can add to the cost.
- Barrier Properties:
- Pouches with advanced barrier properties, such as those designed for extended shelf life or high resistance to environmental factors, may be more expensive.
- Sustainability Considerations:
- If using eco-friendly or sustainable materials is a priority, it may impact the cost of the pouch.
- Supplier/Manufacturer:
- Different suppliers or manufacturers may have varying cost structures. Factors such as production capabilities, technology, and geographic location can influence pricing.
It's important for businesses to work closely with packaging suppliers or manufacturers to discuss their specific requirements, obtain quotes, and understand the factors contributing to the overall cost. Additionally, considering the balance between packaging costs, product quality, and overall brand strategy is crucial for making informed decisions about frozen food packaging pouches.
The process of Mechanized packaging bag for frozen food
Mechanized packaging of frozen food involves the use of automated machinery to streamline the packaging process. This process ensures efficiency, accuracy, and consistency in packaging frozen food products. Here's an overview of the mechanized packaging process for frozen food:
- Product Preparation:
- Frozen food products are prepared for packaging. This may involve portioning, sorting, and arranging the products for efficient handling by the packaging machinery.
- Automated Weighing and Portioning:
- Automated weighing systems measure precise portions of frozen food products. This ensures accurate portion control and consistency in each package.
- Product Conveyance:
- Mechanized conveyor systems transport the weighed and portioned frozen food products to the packaging station. Conveyors are designed to handle frozen products efficiently.
- Bag Forming:
- Automated bag-forming equipment creates the packaging bags from rolls of packaging material. The bags are formed and held open for filling.
- Filling and Sealing:
- The portioned frozen food products are mechanically deposited into the open bags. The bags are then sealed using automated sealing equipment. Common sealing methods include heat sealing, ultrasonic sealing, or vacuum sealing.
- Labeling and Coding:
- Automated labeling and coding systems apply product labels and date codes to the sealed bags. This ensures proper product identification and traceability.
- Quality Inspection:
- Mechanized inspection systems may be integrated to check the sealed bags for any defects, ensuring that the packaging meets quality standards.
- Metal Detection:
- Some mechanized packaging lines include metal detection systems to identify and reject any packages that may contain metal contaminants.
- Weighing and Checkweighing:
- Automated checkweighers verify that each packaged product meets the specified weight criteria. Any underweight or overweight packages are rejected.
- Secondary Packaging (Optional):
- In some cases, mechanized systems may handle the secondary packaging of multiple primary packages into larger cartons or cases for distribution.
- Palletizing:
- Automated palletizing systems arrange the packaged products on pallets for efficient storage and transportation. Robots or automated arms may be used for palletizing.
- Stretch Wrapping (Optional):
- Mechanized stretch wrapping machines may be used to secure and stabilize the palletized products for transit.
- Storage and Distribution:
- The palletized and wrapped products are stored in refrigerated or frozen storage facilities before being distributed to retailers or other points of sale.
The mechanized packaging process for frozen food is designed to minimize manual labor, increase production efficiency, and maintain the quality and integrity of the frozen products. The level of automation and the specific equipment used can vary based on the scale of production and the types of frozen food products being packaged.
Is shrink wrap frozen food packaging better?
Whether shrink wrap is a better packaging option for frozen food depends on various factors, including the specific requirements of the product, distribution considerations, and the overall goals of the packaging. Here are some advantages and considerations for using shrink wrap for frozen food packaging:
Advantages:
- Visual Appeal:
- Shrink wrap provides a visually appealing and professional presentation. It tightly conforms to the shape of the frozen food bags, enhancing the overall appearance.
- Tamper-Evidence:
- Shrink wrap provides a tamper-evident seal, ensuring that the package hasn't been opened or tampered with during storage or transportation.
- Protection Against Contaminants:
- The tight seal created by shrink wrap helps protect frozen food from contaminants, maintaining product quality and safety.
- Space Efficiency:
- Shrink-wrapped packages are often compact, providing space efficiency during storage and transportation. This can be beneficial for maximizing shelf space or optimizing pallet loads.
- Branding Opportunities:
- Shrink wrap allows for high-quality printing, providing opportunities for branding, product information, and promotional messaging directly on the packaging.
- Cost-Effective:
- Shrink wrapping can be a cost-effective packaging solution, especially for bundling multiple items together. It reduces the need for additional packaging materials.
- Conformity to Shape:
- Shrink wrap conforms closely to the shape of the packaged items, creating a snug fit that minimizes excess packaging material.
Considerations:
- Heat Sensitivity of Contents:
- Some frozen food products may be sensitive to heat. The heat applied during the shrink wrapping process should be carefully controlled to prevent any adverse effects on the product.
- Need for Additional Protection:
- Shrink wrap may not provide sufficient protection for certain types of frozen food that require extra insulation or barrier properties. In such cases, additional packaging, such as insulated pouches or boxes, may be necessary.
- Environmental Considerations:
- While shrink wrap can be cost-effective, it is typically made from plastic materials, which may raise environmental concerns. Businesses may need to consider eco-friendly packaging alternatives if sustainability is a priority.
- Application Efficiency:
- The efficiency of the shrink wrapping process depends on the type of equipment used and the scale of production. Businesses need to assess whether shrink wrapping aligns with their production capabilities and volume.
- Regulatory Compliance:
- Ensure that the shrink wrap and overall packaging design comply with food safety regulations, labeling requirements, and any specific industry standards.
Ultimately, the suitability of shrink wrap for frozen food packaging depends on the specific needs of the product, the desired presentation, and the broader considerations of the business, including cost-effectiveness and environmental impact. It's advisable for businesses to conduct thorough testing and evaluation before adopting shrink wrap as a primary packaging solution for frozen food.
Is shrink wrap frozen food packaging same as vacuum packaging?
Shrink wrap packaging and vacuum packaging are distinct methods, each with its own process and purpose. While both techniques involve tightly enclosing and sealing products for preservation, they differ in the mechanism used and the outcomes they achieve. Here's a comparison of shrink wrap frozen food packaging and vacuum packaging:
Shrink Wrap Frozen Food Packaging:
- Process:
- Shrink wrap packaging involves using heat to shrink a plastic film tightly around the product or a group of products. The film is usually a polyolefin or PVC material.
- Purpose:
- The primary purposes of shrink wrap packaging include providing a tight and secure seal, enhancing the visual appeal of the product, and offering tamper-evident protection. It is often used for bundling products together or providing a protective layer around individual items.
- Appearance:
- Shrink wrap conforms closely to the shape of the packaged items, resulting in a snug fit. It enhances the visual presentation of the product, allowing for branding, labeling, and promotional messaging directly on the packaging.
- Tamper-Evidence:
- Shrink wrap provides a tamper-evident seal, making it clear if the package has been opened or tampered with.
- Materials:
- Shrink wrap is typically made from plastic materials, and the heat applied during the process causes the film to shrink tightly around the product.
Vacuum Packaging:
- Process:
- Vacuum packaging involves removing air from the packaging to create a vacuum seal. The product is placed in a vacuum bag, and the air is extracted before sealing.
- Purpose:
- The primary purposes of vacuum packaging include extending the shelf life of perishable products by reducing oxygen levels, preventing freezer burn in frozen foods, and protecting products from external contaminants.
- Preservation:
- Vacuum packaging helps slow down the oxidation and deterioration of food by removing air, which contains oxygen. It is commonly used for preserving the freshness of a variety of products, including meats, cheeses, and vegetables.
- Appearance:
- Vacuum packaging results in a more compact and flattened appearance of the product due to the removal of air. While it provides protection, it may not offer the same visual appeal as shrink wrap.
- Materials:
- Vacuum packaging materials include vacuum bags or pouches made from a variety of materials, including multilayer films with barrier properties.
In summary, while both shrink wrap and vacuum packaging involve tightly sealing products, their methods and purposes differ. Shrink wrap is more focused on visual appeal, tamper-evidence, and bundling, while vacuum packaging is primarily aimed at extending shelf life, preventing freezer burn, and preserving the freshness of perishable items. The choice between the two depends on the specific goals and requirements of the packaging application.
Is it better to freezer bag or vacuum seal?
Whether it is better to use a freezer bag or vacuum seal depends on the specific needs and requirements of the food items being stored. Both methods offer benefits, and the choice depends on factors such as preservation goals, convenience, and the nature of the food. Here's a comparison:
Freezer Bag:
- Convenience:
- Freezer bags are convenient and easy to use. They are available in various sizes and are typically resealable, allowing for easy access to the contents.
- Cost:
- Freezer bags are generally more cost-effective than vacuum sealing equipment. They are widely available and come in multipacks, making them an economical choice.
- Space Efficiency:
- Freezer bags are flexible and can conform to the shape of the food items. They take up less space in the freezer compared to rigid vacuum-sealed packages.
- Suitability for Liquid Items:
- Freezer bags are suitable for storing liquid items as they can be sealed without removing all the air. However, proper sealing is crucial to prevent freezer burn.
- Quick Freezing:
- Food items can be quickly placed in freezer bags and stored in the freezer without the need for additional equipment or preparation.
Vacuum Seal:
- Extended Shelf Life:
- Vacuum sealing removes air from the packaging, reducing the risk of freezer burn and extending the shelf life of the food. This is particularly beneficial for long-term storage.
- Preservation of Freshness:
- Vacuum sealing helps preserve the freshness, flavor, and texture of the food by minimizing exposure to air and preventing oxidation.
- Prevention of Freezer Burn:
- Vacuum-sealed packages provide a more effective barrier against freezer burn, which can occur when air comes into contact with frozen food.
- Space Efficiency:
- Vacuum-sealed packages can be more space-efficient in the freezer, as the removal of air results in a more compact storage form.
- Protection Against Odors:
- Vacuum sealing helps protect food from absorbing odors from other items in the freezer, maintaining the integrity of the flavors.
Considerations:
- Type of Food:
- The type of food being stored influences the choice. Vacuum sealing is particularly advantageous for items prone to freezer burn, such as meats and delicate foods.
- Duration of Storage:
- For short-term storage, a freezer bag may be sufficient. For long-term storage, vacuum sealing provides additional benefits in terms of preservation.
- Equipment Cost:
- Vacuum sealing requires specialized equipment, which may involve an upfront cost. Consider the budget and frequency of use when deciding on the method.
- Convenience vs. Preservation Goals:
- While freezer bags are convenient, vacuum sealing is chosen when the primary goal is to extend the shelf life and preserve the quality of the food.
Ultimately, the choice between a freezer bag and vacuum sealing depends on individual preferences, storage goals, and the specific characteristics of the food items being stored. Some individuals may use a combination of both methods based on their needs.