In the realm of product packaging, the choice of the right packaging material is pivotal to a product's success. Powder packaging bags have become a staple for a wide range of industries, offering a myriad of benefits that cater to the unique needs of powdery substances. In this blog post, we will explore the various aspects that make powder packaging bags indispensable in today's manufacturing landscape.
Section 1: The Importance of Effective Powder Packaging
The first impression of a product often comes from its packaging. Powder packaging bags play a crucial role in not only protecting the contents from external factors but also in attracting consumers with their visual appeal. From food and pharmaceuticals to industrial chemicals, the right powder packaging can make all the difference in product presentation and preservation.
Section 2: Variety in Material Selection
Powder packaging bags come in a variety of materials, each tailored to meet specific needs. Common materials include polyethylene, polypropylene, and laminated films, each chosen based on factors such as product sensitivity, durability requirements, and environmental considerations. Manufacturers can select the material that aligns best with their product characteristics.
Section 3: Customization for Branding and Information
One of the standout features of powder packaging bags is the ability to customize them according to branding requirements and regulatory information. Companies can incorporate vibrant designs, logos, and essential product details, creating a visually appealing package that communicates vital information to consumers.
Section 4: Barrier Properties for Product Preservation
The effectiveness of powder packaging bags is amplified by their barrier properties. These bags are designed to provide a protective shield against moisture, oxygen, light, and contaminants. This ensures the integrity and freshness of the powdered product, extending its shelf life and maintaining quality from production to consumption.
Section 5: Sustainable Packaging Practices
As sustainability becomes a driving force in consumer choices, powder packaging bags have adapted to meet eco-friendly standards. Many manufacturers offer options made from recyclable materials, contributing to a reduction in environmental impact. Sustainable practices in packaging not only benefit the planet but also resonate positively with environmentally conscious consumers.
Section 6: Convenience Features for End-Users
Powder packaging bags are not just about protection; they also prioritize user convenience. Resealable closures, tear notches, and easy-to-open features make these bags user-friendly, ensuring that consumers can access the powdered contents with ease while preserving freshness and preventing spillage.
Conclusion:
Powder packaging bags represent the epitome of functional and visually appealing packaging solutions. Their versatility, barrier properties, and sustainability make them an essential choice for manufacturers across diverse industries. By selecting the right powder packaging bags, companies can not only enhance the appeal of their products but also ensure the longevity and quality of the powders they contain.
How to Custom powder bags?
Customizing powder bags involves several steps to ensure that the final product meets your specific requirements and aligns with your branding. Here's a general guide on how to customize powder bags:
- Define Your Requirements:
- Clearly outline your requirements and specifications. Consider factors such as bag size, material, closure type, and any specific features you need, such as tear notches, resealable zippers, or spouts.
- Choose the Right Material:
- Select a material that suits your product and its characteristics. Different powders may have varied sensitivities to factors like moisture and light. Common materials for powder bags include polyethylene, polypropylene, and laminated films.
- Design Your Artwork:
- Work on the design of your powder bag. This involves incorporating your brand logo, colors, product information, and any other relevant details. Make sure the design aligns with your overall branding strategy.
- Select Printing Options:
- Decide on the printing options for your custom powder bags. Common printing methods include flexography, gravure, and digital printing. Choose a method that suits your design complexity and budget.
- Consider Sustainability:
- If environmental sustainability is a priority, opt for eco-friendly materials and printing processes. Many manufacturers now offer recyclable or biodegradable options for powder bags.
- Choose Closure and Sealing Mechanisms:
- Decide on the type of closure and sealing mechanisms you want for your powder bags. Options include heat-sealing, resealable zippers, or spouts, depending on the nature of your product and how end-users will interact with it.
- Work with a Packaging Manufacturer:
- Partner with a reputable packaging manufacturer or supplier who specializes in custom packaging. Provide them with your specifications, design files, and any other relevant details. They can guide you on the feasibility of your design and offer recommendations based on their expertise.
- Review Prototypes:
- Before mass production, request prototypes or samples of your custom powder bags. This allows you to physically assess the design, material, and functionality, ensuring that it meets your expectations.
- Test for Product Compatibility:
- If your powder has specific characteristics or requirements, conduct tests to ensure compatibility with the chosen packaging material. This is especially important for food or pharmaceutical powders where maintaining product integrity is crucial.
- Finalize and Proceed to Production:
- Once you are satisfied with the prototypes and have addressed any necessary adjustments, finalize the design and proceed with mass production.
- Quality Control:
- Implement quality control measures during production to ensure that each batch of custom powder bags meets your standards. This includes checking for print quality, sealing integrity, and overall durability.
By carefully following these steps and working closely with a packaging manufacturer, you can create custom powder bags that not only protect your product but also serve as an effective branding tool.
Which material is most suitable to flexible powder packaging bag?
The choice of material for flexible powder packaging bags depends on various factors, including the type of powder, product sensitivity, barrier requirements, and sustainability considerations. Here are some commonly used materials for flexible powder packaging bags:
- Polyethylene (PE):
- Advantages:
- Lightweight and flexible.
- Resistant to moisture.
- Cost-effective.
- Recyclable.
- Considerations:
- May not provide the highest barrier properties.
- Advantages:
- Polypropylene (PP):
- Advantages:
- Strong and durable.
- Resistant to moisture and chemicals.
- Good heat resistance.
- Recyclable.
- Considerations:
- Slightly less flexible than polyethylene.
- Advantages:
- Polyester (PET):
- Advantages:
- High clarity and gloss.
- Good tensile strength.
- Resistant to moisture.
- Recyclable.
- Considerations:
- May not be as flexible as polyethylene.
- Advantages:
- Nylon (PA):
- Advantages:
- Strong and puncture-resistant.
- High barrier properties.
- Good heat resistance.
- Considerations:
- Relatively higher cost.
- Limited recyclability.
- Advantages:
- Metallized Films:
- Advantages:
- Improved barrier properties (against light, oxygen, and moisture).
- Enhanced shelf life for sensitive powders.
- Considerations:
- Can be less environmentally friendly.
- Advantages:
- Laminated Films:
- Advantages:
- Combine multiple layers for enhanced properties.
- Customizable for specific barrier requirements.
- Considerations:
- The complexity may increase costs.
- Advantages:
- Biodegradable and Compostable Films:
- Advantages:
- Environmentally friendly.
- Suitable for certain powders.
- Considerations:
- Limited availability and may have specific disposal requirements.
- Advantages:
When selecting a material for your flexible powder packaging bags, consider the following:
- Barrier Properties: Depending on the sensitivity of the powder to factors like moisture, oxygen, and light, choose a material with appropriate barrier properties.
- Product Compatibility: Some powders may interact with certain materials, affecting product quality. Conduct compatibility tests if necessary.
- Regulatory Compliance: Ensure that the chosen material complies with relevant regulations, especially if packaging food, pharmaceuticals, or other regulated products.
- Sustainability Goals: If sustainability is a priority, consider materials that are recyclable or made from renewable resources.
Ultimately, the best material for your flexible powder packaging bag will depend on the specific requirements of your product and your overall packaging objectives. Working with a packaging expert or supplier can help you make an informed decision based on your unique needs.
Which bag types are the most suitable to flexible powder packaging bag?
Several bag types are suitable for flexible powder packaging, each with its unique features and advantages. The choice of bag type depends on factors such as the nature of the powder, packaging requirements, and user convenience. Here are some common types of flexible powder packaging bags:
- Stand-Up Pouches:
- Features:
- Self-standing design.
- Often equipped with resealable zippers for easy access.
- Available with various closure options (press-to-close, ziplock, etc.).
- Suitability:
- Suitable for a wide range of powders.
- Ideal for retail packaging.
- Features:
- Flat Pouches:
- Features:
- Flat, compact design.
- Often used for single-use or small quantity packaging.
- Can be heat-sealed or include resealable options.
- Suitability:
- Suitable for powders with moderate use frequency.
- Commonly used in sample or travel-sized packaging.
- Features:
- Gusseted Bags:
- Features:
- Expandable sides (gussets) for increased volume.
- May have a bottom gusset for stability.
- Suitable for bulk packaging.
- Suitability:
- Ideal for packaging larger quantities of powder.
- Features:
- Quad Seal Bags:
- Features:
- Four-panel construction for added strength and stability.
- Suitable for heavy or bulk powders.
- Often used for premium or high-end products.
- Suitability:
- Suitable for powders with higher weight/volume.
- Features:
- Spout Pouches:
- Features:
- Include a spout for controlled pouring or dispensing.
- Often used for liquids but can be adapted for powders.
- Convenient and mess-free.
- Suitability:
- Suitable for powders that require controlled pouring.
- Features:
- Sachets:
- Features:
- Small, sealed packets.
- Single-use or small quantity packaging.
- Easy to tear open.
- Suitability:
- Ideal for single-serve or on-the-go packaging.
- Features:
- Bulk Bags (FIBC - Flexible Intermediate Bulk Container):
- Features:
- Large bags for bulk powder storage and transportation.
- Often used in industrial settings.
- Multiple lifting and discharge options.
- Suitability:
- Ideal for bulk storage and transportation of powdered products.
- Features:
- Three-Side Seal Bags:
- Features:
- Sealed on three sides with one open side.
- Can be heat-sealed or include reclosable options.
- Suitability:
- Versatile and suitable for various powders.
- Features:
When choosing a bag type for flexible powder packaging, consider factors such as the volume of powder, ease of use, shelf presentation, and any specific dispensing requirements. Working closely with a packaging specialist can help you determine the most suitable bag type for your specific application.
Will the bag react chemically with the inside contents? and how to avoid?
The potential for a bag to react chemically with the contents inside depends on various factors, including the type of material used for the bag and the nature of the contents. Here are some considerations to help you assess the potential for chemical reactions:
- Material Compatibility:
- Different packaging materials have different chemical properties. For example, certain plastics may interact with specific chemicals, leading to leaching or degradation. It's crucial to select a packaging material that is compatible with the type of powder you are packaging.
- Barrier Properties:
- Consider the barrier properties of the packaging material. Some materials provide a better barrier against external factors like moisture, oxygen, and light, which can impact the chemical stability of the contents.
- Product Sensitivity:
- The sensitivity of the powder to external factors is an important consideration. If the powder is reactive or prone to degradation, choosing a packaging material with excellent barrier properties and chemical resistance is essential.
- Regulatory Compliance:
- Ensure that the packaging material complies with relevant regulations, especially if you are packaging food, pharmaceuticals, or other regulated products. Regulatory bodies may have specific requirements for packaging materials to ensure product safety.
- Testing and Compatibility Studies:
- Conduct compatibility studies between the powder and the selected packaging material. This can involve testing the packaged product over time to ensure there are no adverse reactions. Such studies are particularly important for sensitive products.
- Packaging Additives:
- Some packaging materials may contain additives or coatings that could potentially interact with the contents. Be aware of any additional layers or treatments applied to the packaging material and assess their compatibility.
- pH Levels:
- Consider the pH levels of both the powder and the packaging material. Some materials may be more prone to chemical reactions in acidic or alkaline environments.
- Temperature Sensitivity:
- Some powders may generate heat or be sensitive to temperature changes, potentially leading to chemical reactions with the packaging material. Choose a material that can withstand the expected temperature conditions during storage and transportation.
- Consultation with Packaging Experts:
- Seek advice from packaging experts or suppliers who specialize in the type of material you are considering. They can provide insights into the chemical compatibility of their products.
It's essential to thoroughly research and understand the characteristics of both the powder and the chosen packaging material. Additionally, conducting compatibility testing and seeking professional advice can help ensure that the packaging does not react chemically with the contents and maintains the product's integrity.
Can the powder bag be made to a vacuum bag?
Yes, powder bags can be designed as vacuum bags. Vacuum packaging is a method where air is removed from the package to create a vacuum, which helps preserve the product by reducing the oxygen content. This process is commonly used for extending the shelf life of various products, including powders. Here are some considerations for creating vacuum powder bags:
- Selecting the Right Material:
- Choose packaging materials with good barrier properties to maintain the vacuum and protect the powder from external factors. Common materials for vacuum bags include multilayer films with properties such as high oxygen and moisture barrier.
- Vacuum Sealing Technology:
- Ensure that the bags are equipped with reliable vacuum sealing technology. This may include heat-sealing processes or specialized vacuum sealing equipment that removes air from the bag before sealing.
- Durability and Puncture Resistance:
- Vacuum packaging often involves removing air, which can create pressure on the packaging material. Select materials that are durable and puncture-resistant to prevent the loss of vacuum during handling and transportation.
- Seal Integrity:
- The seal of the vacuum bag must be airtight to maintain the vacuum effect. Consider features such as heat-sealed seams or specialized closures that enhance seal integrity.
- Valves for Controlled Vacuuming:
- Some vacuum bags come with one-way valves that allow controlled release of air and facilitate efficient vacuuming. These valves help maintain the vacuum seal while preventing air from re-entering the bag.
- Packaging Design:
- Design the bag to accommodate the vacuum process. This may include leaving enough space within the bag for the powder to expand slightly when the vacuum is created.
- Testing and Quality Assurance:
- Conduct rigorous testing to ensure that the vacuum bags maintain their seal and preserve the contents effectively. Quality assurance measures are crucial to guarantee the reliability of the vacuum packaging.
- User-Friendly Features:
- Consider incorporating user-friendly features, such as resealable zippers or tear notches, to make it easy for end-users to access the powdered product while preserving the vacuum seal after opening.
- Regulatory Compliance:
- Ensure that the vacuum bags comply with relevant regulations, especially if you are packaging food or pharmaceutical powders.
By integrating vacuum packaging features into powder bags, you can enhance the shelf life of the powdered product and maintain its quality by minimizing exposure to oxygen and moisture. Working with experienced packaging manufacturers and suppliers can help ensure that your vacuum powder bags meet industry standards and effectively preserve your product.
Which bag materials and types will be suitable to milk powder packaging?
Milk powder is a sensitive product that requires careful consideration when choosing packaging materials. The packaging must protect the powder from moisture, light, and oxygen to maintain its quality. Here are suitable bag materials and types for milk powder packaging:
1. Material Options:
a. Multilayer Barrier Films: - Multilayer films, often composed of materials like polyethylene, polyester, and aluminum, provide excellent barrier properties against moisture, oxygen, and light. These films help preserve the freshness and flavor of milk powder.
b. Metalized Films: - Metalized films, with a thin layer of metal (usually aluminum), offer enhanced barrier properties. They provide a strong barrier against light and oxygen, contributing to the product's shelf life.
c. Laminated Films: - Laminated films combine multiple layers for improved strength and barrier properties. Common laminations include combinations of polyethylene, polyester, and metalized layers.
d. Polyethylene (PE) and Polyethylene Terephthalate (PET): - These materials are often used in combination to create packaging films with good seal strength and barrier properties. They are suitable for milk powder packaging, especially when combined in multilayer structures.
2. Bag Types:
a. Stand-Up Pouches: - Stand-up pouches are convenient and provide a large printable surface for branding. They often come with resealable zippers, ensuring that the milk powder remains fresh after opening.
b. Flat Pouches: - Flat pouches are simple and cost-effective. They are suitable for single-use or smaller quantities of milk powder. Heat-sealable options are common for these pouches.
c. Quad Seal Bags: - Quad seal bags have a four-panel construction that provides stability and ample space for branding. They are suitable for larger quantities of milk powder.
d. Tin-Tie Bags: - Tin-tie bags have a resealable feature, often used for coffee packaging. They can be adapted for milk powder, allowing for easy opening and resealing.
e. Gusseted Bags: - Gusseted bags have expandable sides, making them suitable for bulk packaging. They can accommodate larger volumes of milk powder.
f. Vacuum Sealed Bags: - Vacuum-sealed bags help extend the shelf life of milk powder by removing air and reducing the risk of oxidation. These bags often use multilayer barrier films for effective protection.
g. Spout Pouches: - Spout pouches with a resealable spout are convenient for controlled pouring of milk powder. They offer a mess-free solution for users.
3. Additional Considerations:
- Regulatory Compliance:
- Ensure that the chosen materials and packaging types comply with relevant food safety regulations, especially if packaging milk powder for human consumption.
- Product Information and Branding:
- Consider including important product information, instructions, and branding on the packaging to enhance consumer understanding and trust.
- Sustainability:
- If sustainability is a priority, explore options for eco-friendly packaging materials or consider communicating the recyclability of the packaging to environmentally conscious consumers.
When selecting packaging materials and types for milk powder, it's crucial to conduct thorough testing to ensure the chosen packaging effectively preserves the product's quality throughout its shelf life. Consulting with packaging experts and suppliers with experience in dairy product packaging can provide valuable insights for making informed decisions.
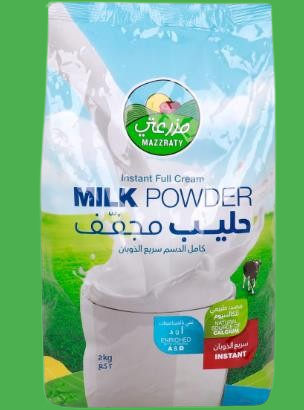
Which bag materials and types will be suitable to red powder packaging? such as red spice packaging? turmeric powder packaging?
When packaging red powders, such as spices, it's important to choose materials and bag types that not only protect the contents from external factors like moisture and light but also enhance the overall visual appeal. Here are suitable bag materials and types for red powder packaging:
1. Material Options:
a. Polyethylene (PE) and Polypropylene (PP): - PE and PP films are commonly used for spice packaging. They offer good moisture resistance and are cost-effective. Additionally, they can be transparent or opaque, allowing for visibility of the product.
b. Metalized Films: - Metalized films, typically with an aluminum layer, provide enhanced barrier properties against light and oxygen. This helps in preserving the color, flavor, and aroma of red spices.
c. Polyester (PET): - PET films offer good clarity and are suitable for packaging red powders. They provide a smooth surface for high-quality printing and can be combined with other materials for enhanced barrier properties.
d. Laminated Films: - Laminated films, combining multiple layers such as polyethylene, polyester, and metalized layers, can provide a balance of strength and barrier properties. This is beneficial for protecting red spices from environmental factors.
2. Bag Types:
a. Stand-Up Pouches: - Stand-up pouches are popular for spice packaging due to their versatility and visual appeal. They provide ample space for branding and can include features like resealable zippers.
b. Flat Bottom Bags (Box Pouches): - Flat bottom bags offer stability and a unique presentation. They stand upright on store shelves and are suitable for premium red spice packaging.
c. Flat Pouches: - Flat pouches are simple and cost-effective. They are suitable for smaller quantities of red spices and can be heat-sealed for freshness.
d. Quad Seal Bags: - Quad seal bags have a four-panel construction that provides stability and space for branding. They are suitable for larger quantities of red spices.
e. Spout Pouches: - Spout pouches are convenient for pouring and dispensing red spices. They can include resealable spouts to maintain freshness.
f. Gusseted Bags: - Gusseted bags have expandable sides, making them suitable for bulk red spice packaging. They provide ample space for product information and branding.
3. Additional Considerations:
- Light Protection:
- Ensure that the chosen material provides sufficient protection against light to prevent the degradation of color in red spices. Metalized films or opaque materials are effective for light protection.
- Heat Sealability:
- If the packaging needs to be heat-sealed for freshness, choose materials that allow for effective heat sealing.
- Barrier Properties:
- Consider the barrier properties of the chosen material to protect red spices from moisture, oxygen, and other environmental factors.
- Printability:
- Select materials that allow for high-quality printing to showcase product information and branding effectively.
- Regulatory Compliance:
- Ensure that the chosen materials comply with food safety regulations, especially when packaging spices for human consumption.
Selecting the right combination of materials and bag types is crucial to ensuring that red spice packaging not only preserves the product's quality but also attracts consumers with its visual appeal. Conducting compatibility tests and consulting with packaging experts can help make informed decisions based on the specific requirements of the red spice product.
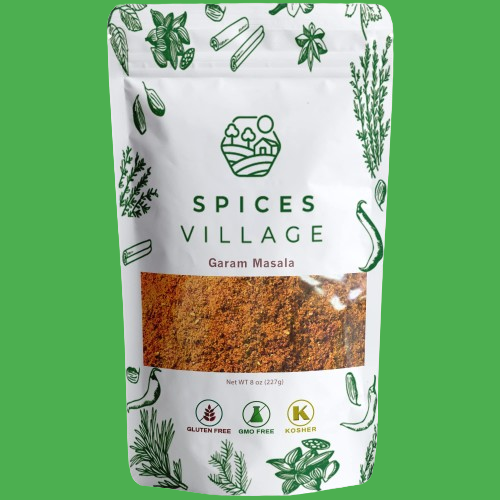
Which bag materials and types will be suitable to protein powder bag?
When packaging protein powder, it's essential to choose materials and bag types that provide effective protection against moisture, light, and oxygen to maintain the product's freshness and quality. Here are suitable bag materials and types for protein powder packaging:
1. Material Options:
a. Polyethylene (PE) and Polypropylene (PP): - PE and PP films are commonly used for protein powder packaging. They offer good moisture resistance and are cost-effective. PE is often chosen for its flexibility, while PP provides a stiffer structure.
b. Polyester (PET): - PET films offer good clarity and are suitable for packaging protein powder. They provide a smooth surface for high-quality printing and are commonly used in laminated structures for enhanced barrier properties.
c. Metalized Films: - Metalized films, typically with an aluminum layer, provide excellent barrier properties against light and oxygen. This is beneficial for preserving the nutritional content and quality of protein powder.
d. Laminated Films: - Laminated films, combining multiple layers such as polyethylene, polyester, and metalized layers, can offer a balance of strength and barrier properties. This is important for protecting protein powder from environmental factors.
2. Bag Types:
a. Stand-Up Pouches: - Stand-up pouches are popular for protein powder packaging due to their convenience and visual appeal. They provide a large printable surface for branding and often include resealable features like zippers.
b. Flat Bottom Bags (Box Pouches): - Flat bottom bags offer stability and an attractive presentation on store shelves. They stand upright and are suitable for premium protein powder packaging.
c. Flat Pouches: - Flat pouches are simple and cost-effective. They are suitable for single-use or smaller quantities of protein powder and can be heat-sealed for freshness.
d. Quad Seal Bags: - Quad seal bags have a four-panel construction that provides stability and space for branding. They are suitable for larger quantities of protein powder.
e. Spout Pouches: - Spout pouches are convenient for controlled pouring and dispensing of protein powder. They can include resealable spouts to maintain freshness.
f. Gusseted Bags: - Gusseted bags have expandable sides, making them suitable for bulk packaging of protein powder. They provide ample space for product information and branding.
3. Additional Considerations:
- Moisture Resistance:
- Ensure that the chosen material provides effective moisture resistance to protect the protein powder from clumping and degradation.
- Oxygen Barrier:
- Select materials with excellent oxygen barrier properties to preserve the freshness and nutritional content of the protein powder.
- Printability:
- Choose materials that allow for high-quality printing to showcase product information, usage instructions, and branding effectively.
- Resealable Features:
- Consider packaging with resealable features such as zippers or spouts to allow users to reseal the bag after opening, preserving the product's freshness.
- Regulatory Compliance:
- Ensure that the chosen materials comply with food safety regulations, especially when packaging products intended for human consumption.
By carefully selecting the right combination of materials and bag types, you can ensure that the protein powder remains fresh and high-quality throughout its shelf life. Conducting compatibility tests and consulting with packaging experts can provide valuable insights based on the specific requirements of the protein powder product.
In conclusion, the flexible packaging bag for powder is a commonly used type. For more information, plz kindly feel free to contact us.