Flexible packaging has become increasingly popular in recent years due to its versatility and convenience. Flexible packaging bags are used to package a wide range of products, including food, beverages, pharmaceuticals, and household goods. In this post, we'll take a closer look at the flexible packaging bag making process.
Step 1: Material Selection
The first step in making flexible packaging bags is to select the appropriate materials based on the product being packaged and the desired properties of the packaging. Some of the most common materials used for flexible packaging include plastic films, laminates, foils, and paper.
Here are some of the factors to consider during the packaging bag material selection process:
- Product Compatibility: The packaging material must be compatible with the product being packaged to ensure that it does not negatively affect the product's quality, safety, or shelf life. For example, certain foods may require packaging materials that provide oxygen or moisture barrier properties to maintain freshness.
- Barrier Properties: The packaging material should provide the necessary barrier properties to protect the product from external factors such as light, air, and moisture. This can include using materials that are impermeable to oxygen, water vapor, or UV light.
- Strength and Durability: The packaging material should be strong and durable enough to withstand transportation and handling without tearing, puncturing, or breaking. This is especially important for products that are heavy or have sharp edges.
- Environmental Impact: The packaging material should be selected with the environmental impact in mind. This can include using materials that are recyclable, biodegradable, or made from renewable resources.
- Regulatory Compliance: The packaging material should comply with any regulatory requirements, such as food safety regulations or environmental regulations.
- Cost: The packaging material should be cost-effective and fit within the budget of the packaging project.
Some common packaging bag materials include plastic films, laminates, foils, and paper. Each material has its own unique properties and is suitable for different types of products and applications. By considering these factors and selecting the appropriate packaging bag material, you can ensure that your product is packaged in a high-quality and effective manner.
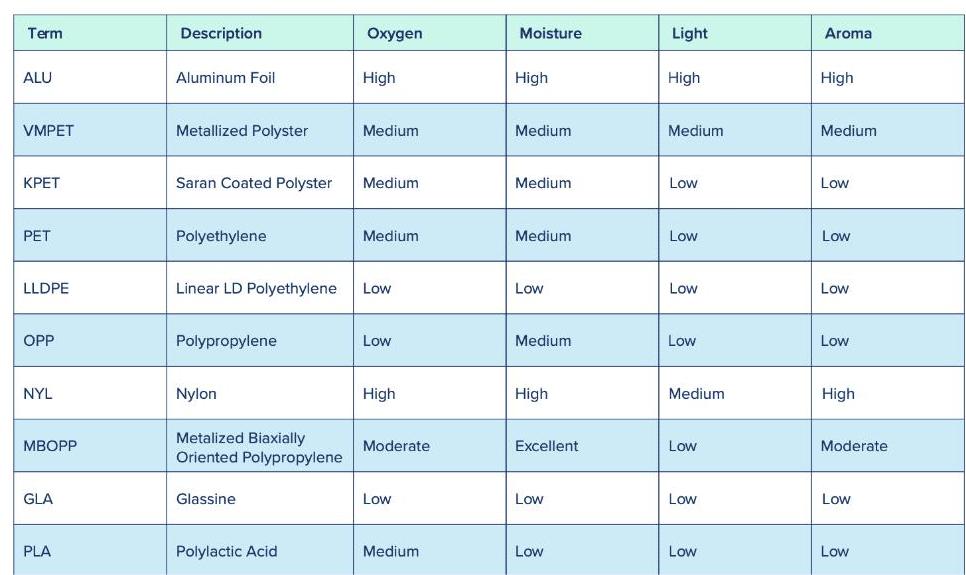
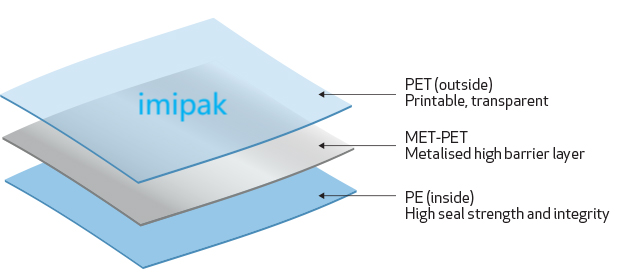
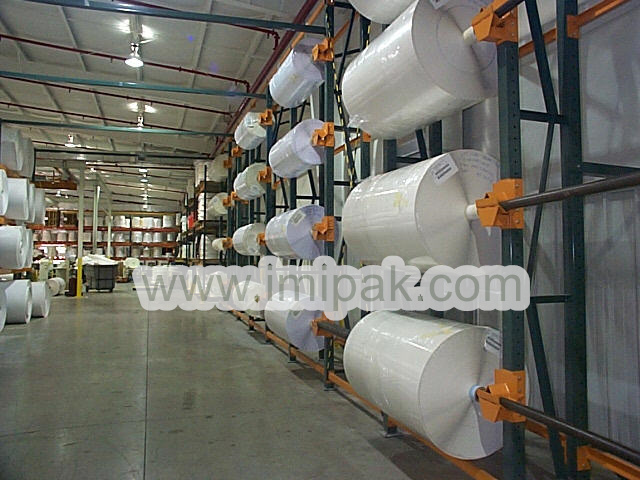
Step 2: Plate Making
The plate making process for packaging bags involves creating a printing plate that is used to transfer the design or branding of the bag onto the laminated material. The plate making process typically involves several stages, including artwork preparation, plate imaging, and plate development.
The first stage of the plate making process is artwork preparation, where the design or branding of the bag is prepared in a digital format. This can be done using various graphic design software programs and involves creating a high-resolution image of the design or branding.
Once the artwork is prepared, it is imaged onto the printing plate. This is typically done using a computer-to-plate (CTP) system, which uses lasers to transfer the digital image onto a light-sensitive coating on the plate. The plate is then exposed to UV light, which hardens the image onto the plate.
After imaging, the plate is developed, which involves removing the unexposed areas of the light-sensitive coating to reveal the image that will be used for printing. This is typically done using a chemical process, which dissolves the unexposed areas of the coating.
The plate making process is critical to the quality and accuracy of the printing on the packaging bag. The quality of the plate and the accuracy of the image transfer will affect the sharpness, clarity, and color accuracy of the final printed image.
Overall, the plate making process is an important step in the production of packaging bags, ensuring that the design or branding of the bag is accurately transferred onto the laminated material.
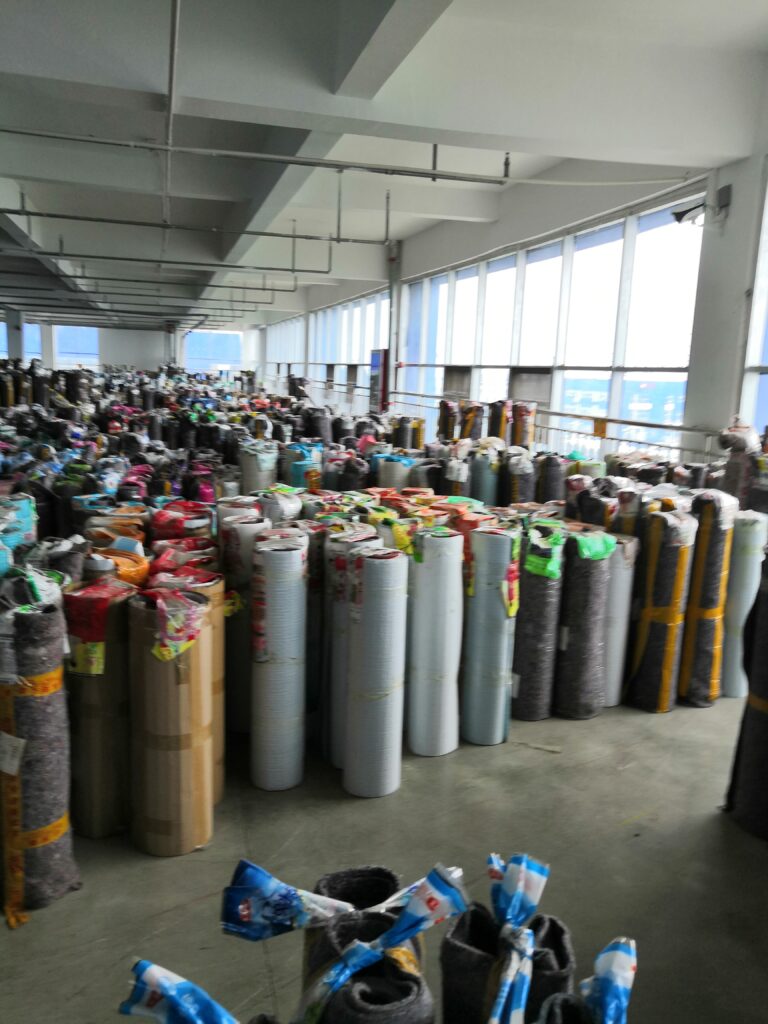
Step 2: Printing
Once the materials are selected, they are printed with designs, logos, and other branding using various printing methods such as flexography, rotogravure, or digital printing.
Here are the steps involved in the packaging bag printing process:
- Pre-Press: This is the preparation phase before printing. It includes design creation, color separation, image preparation, and plate-making. The design is created using specialized software, and color separation is done to ensure accurate color reproduction. The image is then prepared for printing and transferred onto the printing plate.
- Printing: The prepared printing plate is loaded onto the printing press, and the ink is applied to the surface of the packaging material using various printing techniques such as flexography, gravure, or digital printing. The printing press applies pressure to transfer the ink from the printing plate to the packaging material.
- Drying: After printing, the ink must be dried or cured to prevent smudging or smearing. This can be done using heat, air, or UV light.
- Finishing: After drying, the packaging material may undergo various finishing processes, such as lamination, varnishing, or coating, to protect the printing and enhance its appearance.
The packaging bag printing process can be customized to suit specific needs, such as printing on both sides of the material, using special inks or coatings, or incorporating security features like holograms or barcodes.
Effective packaging bag printing can help attract consumer attention, communicate important product information, and enhance brand identity. By understanding the packaging bag printing process, businesses can create high-quality, visually appealing, and informative packaging that helps their products stand out in the market.
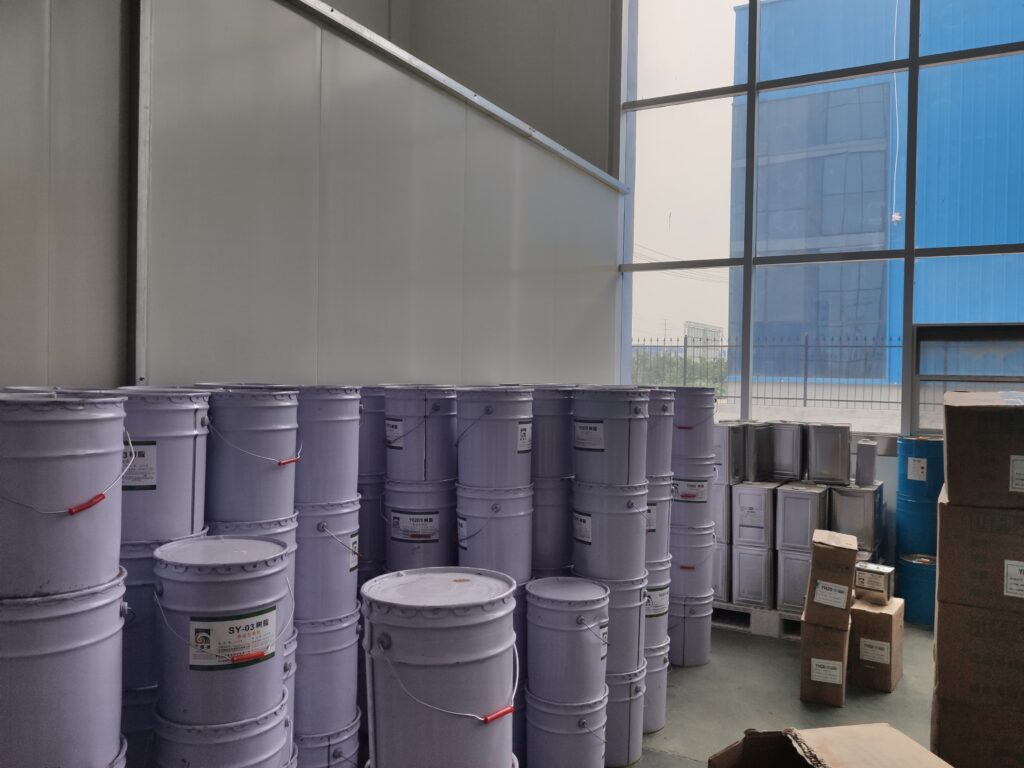
Step 3: Lamination
If required, the printed materials are laminated together to create a multi-layered structure that provides additional strength and barrier properties. Lamination can also improve the overall appearance of the packaging.
Here are the steps involved in the packaging bag lamination process:
- Material Selection: The first step in the lamination process is selecting the appropriate materials to be used in the lamination. This can include films, papers, or foils, which are chosen based on the desired properties of the final product.
- Pre-Treatment: The materials that will be laminated are typically pre-treated to ensure that they are clean, dry, and free of any contaminants. This can include processes such as corona treatment, which increases the surface energy of the materials to improve adhesion.
- Adhesive Application: An adhesive is applied to one or both of the materials that will be laminated together. The adhesive can be applied using various methods such as gravure, flexography, or extrusion coating.
- Lamination: The two or more materials are then brought together and passed through a set of pressure rollers to create a uniform bond between the layers. The temperature and pressure of the rollers are carefully controlled to ensure that the adhesive cures properly and the materials are bonded together securely.
- Slitting and Rewinding: After lamination, the materials are typically slit to the desired width and rewound into rolls for further processing or shipment.
The packaging bag lamination process can be customized based on the specific needs of the application. For example, specialized laminations can be used to provide specific barrier properties such as oxygen, moisture, or light resistance.
Effective lamination can help improve the performance and functionality of flexible packaging materials, making them more durable, strong, and resistant to external factors. By understanding the packaging bag lamination process, businesses can select and produce high-quality, effective packaging solutions for their products.
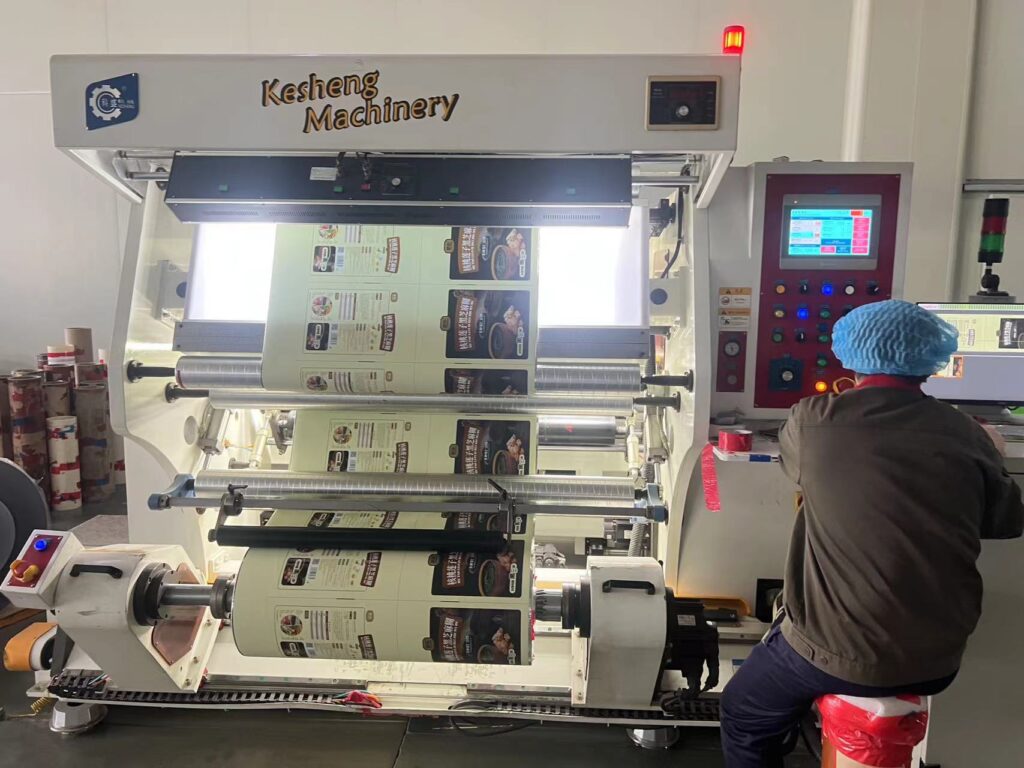
Step 4: Lamination Curing
Lamination is a process in which two or more layers of different materials are combined to create a single, multi-layered structure that provides enhanced properties such as barrier protection, strength, and durability.
The lamination curing process for packaging bags involves applying a layer of adhesive or resin to a substrate, such as paper or plastic, and then bonding it to another layer of substrate. This creates a multi-layered material that provides the necessary strength, durability, and barrier properties required for packaging applications.
The lamination process typically involves three stages: pre-treatment, lamination, and curing. Pre-treatment involves cleaning and preparing the substrate surfaces to ensure proper adhesion. Lamination involves applying the adhesive or resin to one or both substrates and bonding them together. Finally, the curing stage involves heating the laminated material to a specific temperature and for a specific duration to allow the adhesive or resin to fully cure and bond the substrates together.
The curing process is critical to the quality and performance of the final laminated material. The temperature and duration of the curing process are carefully controlled to ensure that the adhesive or resin fully cures and creates a strong bond between the substrates. Improper curing can result in delamination, where the layers of the laminated material separate, reducing the strength and barrier properties of the packaging bag.
Overall, the lamination curing process is a critical step in the production of packaging bags, ensuring that the materials used provide the necessary strength, durability, and barrier properties to protect the contents inside.
Step 5: Slitting
After lamination, the material is slit into narrower rolls to create the desired width for the bags. This step is important as it allows for customization of bag sizes to meet specific product requirements.
here's an overview of the packaging bag slitting process:
- Set up the machine: The slitting machine is set up and calibrated to the specifications of the bag being slit. This includes adjusting the blade, speed, and size of the bag.
- Load the bag: The bag to be slit is loaded onto the machine, usually by placing it onto a conveyor belt that feeds it into the machine.
- Position the bag: The bag is positioned so that the sealed edge is facing down and the top edge is exposed.
- Slit the bag: The machine uses a blade or set of blades to cut open the top edge of the bag. The blade(s) can be adjusted to make a clean cut, without damaging the contents inside the bag.
- Remove the bag: Once the bag is slit, it is removed from the machine and is ready for further processing or use.
- Quality control: The slit bag may be inspected for quality control, to ensure that the cut is clean and that the contents inside the bag are not damaged.
Overall, the packaging bag slitting process is a relatively straightforward process that involves cutting open the top of a sealed bag or pouch to make it easier to access the contents inside. The process is often automated and can be adjusted to the specific needs of the product being packaged.
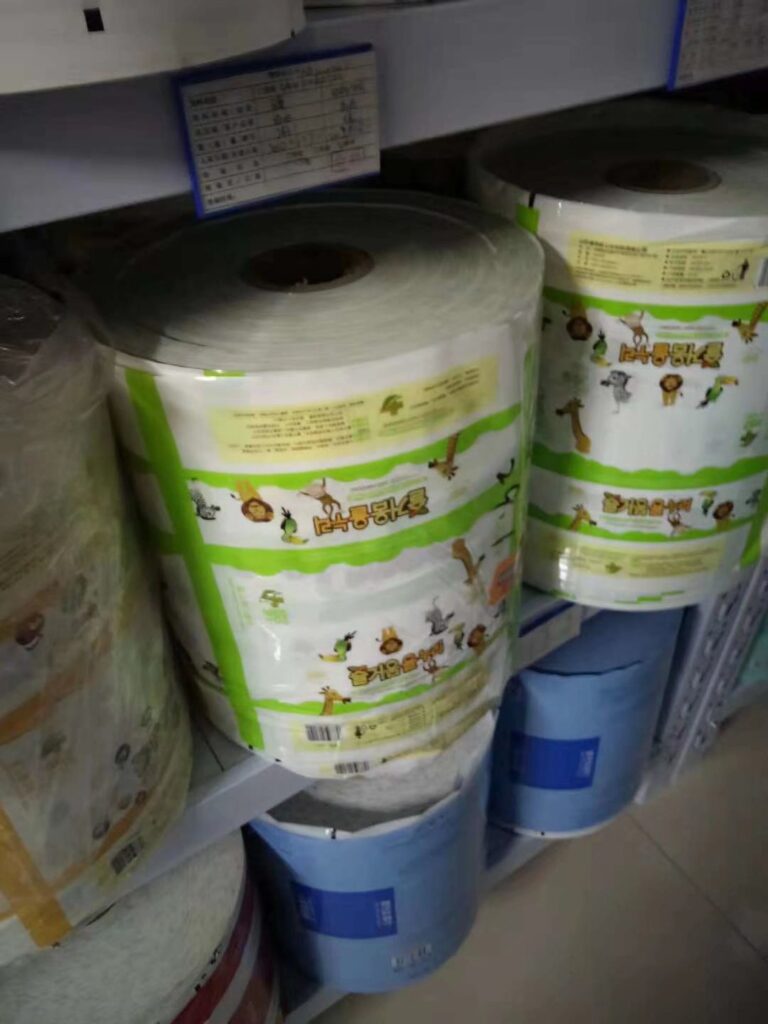
Step 6: Bag Making
The slit rolls are then fed into a bag-making machine, which forms the bags through a series of folding, sealing, and cutting operations. The bags can be made with various features such as resealable zippers, spouts, and handles.
Sure, here's a list of the packaging bag bag making process:
- Printing: The design or branding of the bag is printed onto the laminated material.
- Cutting: The laminated material is cut into the desired shape and size for the bag.
- Folding: The material is folded and shaped into the final bag form, using various folding and shaping techniques depending on the type of bag.
- Sealing: The bag is sealed to close the open edges and create a secure and functional bag, using techniques such as heat sealing, ultrasonic sealing, or adhesive sealing.
- Handle attachment (optional): Handles can be attached to the bag using various methods, including hot stamping, stitching, or gluing.
- Quality control: Throughout the bag making process, quality control checks are performed to ensure that the bags meet the required specifications for strength, durability, and appearance.
- Packaging and shipping: Once the bags have passed quality control, they are packaged and shipped to the customer or end-user.
Overall, the bag making process involves several stages, techniques, and quality control measures to produce a functional, durable, and attractive bag that meets the requirements of the customer.
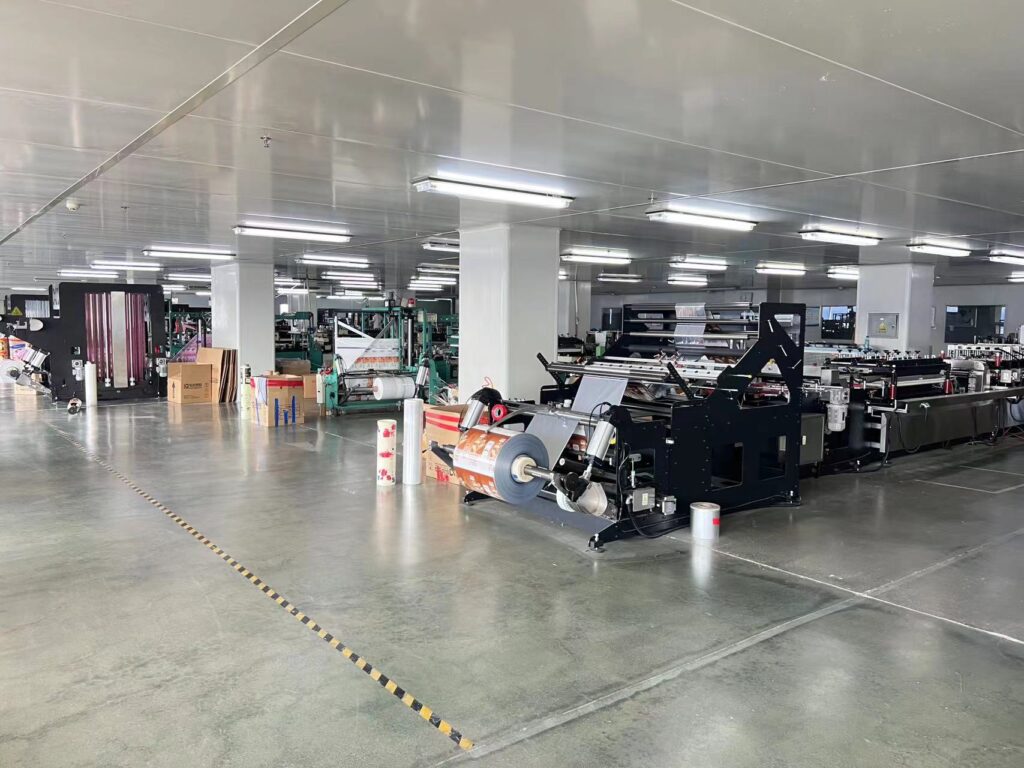
Step 7: Finishing
After the bags are formed, they are finished with additional features such as perforations, embossing, or coatings. These finishing touches can enhance the bag's overall appearance and functionality.
Step 8: Quality Control
Throughout the entire process, quality control checks are performed to ensure the bags meet the desired specifications and standards. Quality control checks can include testing for seal strength, thickness, and overall appearance.
Step 9: Packaging and Shipping
Finally, the finished bags are packaged and shipped to their final destination for use in various industries such as food, pharmaceuticals, or consumer goods.
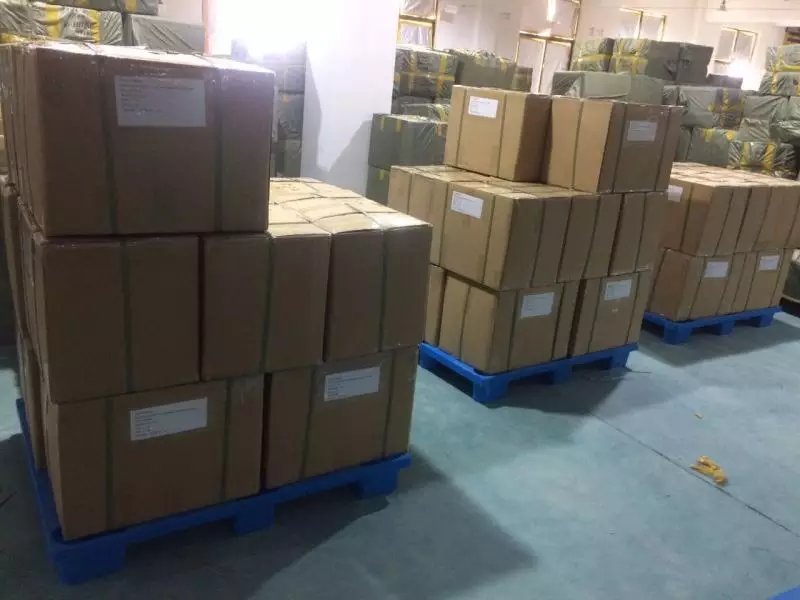
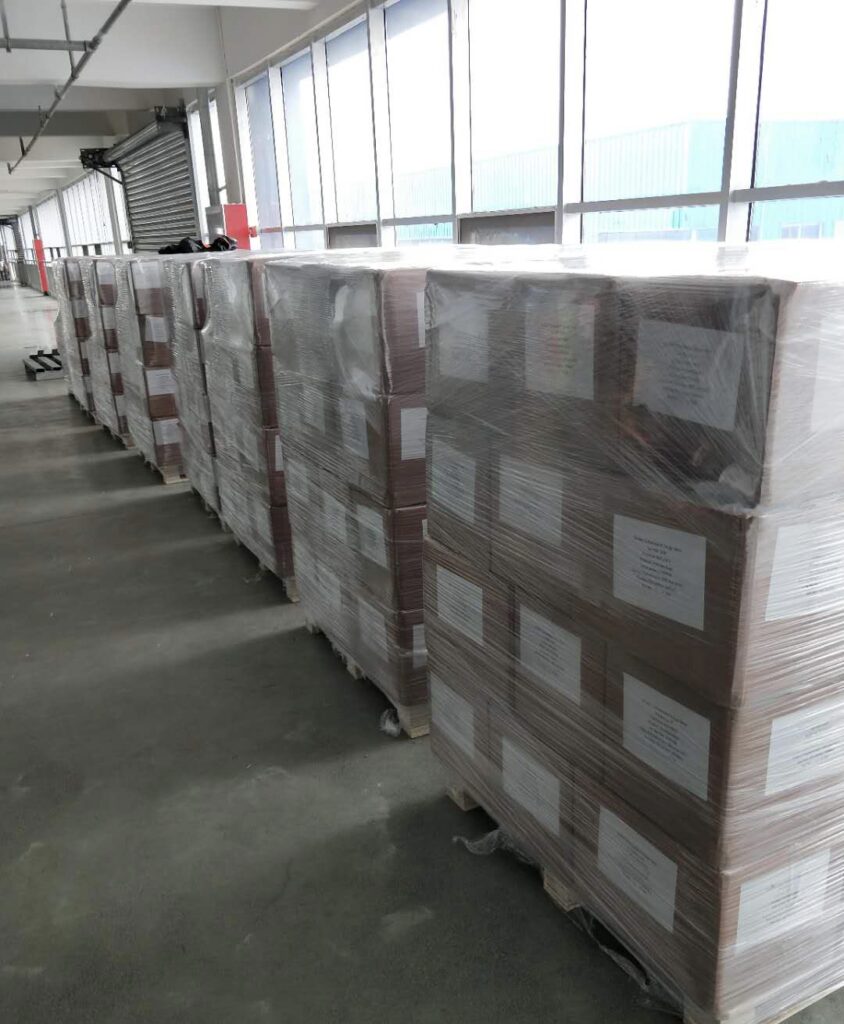
In conclusion, the flexible packaging bag making process involves a series of steps that require careful attention to detail and quality control. The end result is a versatile and convenient packaging solution that can be customized to meet the unique needs of a wide range of products.